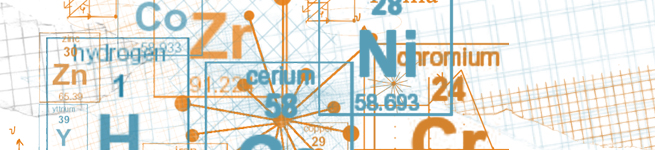
HOTGASYS
Compact hot gas clean-up system for particulate removal
Title of Programme
|
THE FOURTH FRAMEWORK PROGRAMME - JOULE-THERMIE III
R&D tasks in advanced cycles Cost-sharing contracts
|
Financing Code for Project
|
JOF3CT970047
|
Project start year - end year | 1998 - 2000 |
Financing organisation |
EUROPEAN COMMISSION RESEARCH
DIRECTORATE-GENERAL
|
Coordinator | Notox International A/S |
Other partners |
Ceramics and Refractories Technological Development Company S.A. (CERECO)
Technical University of Denmark (DTU)
Ceramiques Techniques et Industriells S.A. (CTI)
Aerosol and Particle Technology Laboratory (APTL)
|
Budget / APTL Budget | 1.980.000,00€ / 360.000,00€ |
Scientific Manager / Project researcher | A. G. Konstandopoulos |
Project website | http://cordis.europa.eu/ |
Summary description |
Advanced power generation cycles from solid fuels can contribute significantly to future European energy security and require particle-clean combustion/gasification product gases at high temperatures in order to achieve at the same time significant energy efficiency and environmental benefits.
State-of-the-art hot gas particle clean-up technology is typically based on ceramic candle filters (rigid and soft), and to a lesser extent on smaller, one piece honeycomb cross-flow filters The technology is still in a stage far from providing reliable and cost-effective particulate removal from hot gases Major problems areas involve: mechanical failure due to ash particle bridging, filter thermal stability and materials compatibility issues, system price due to high candle filter weight and manufacturing cost and appreciable pressure drop, to name a few. The objective of the proposed research is to develop a compact hot gas particulate clean-up system by integrating three specifically tailored, advanced high temperature ceramic materials (Silicon Carbide, high strength Cordierite and Aluminum Titanate) into a novel, and cost-effective filter design, so as to overcome problems with current candle technology. The system to be developed will have the following characteristics compared to a similarly sized candle-based system:
|