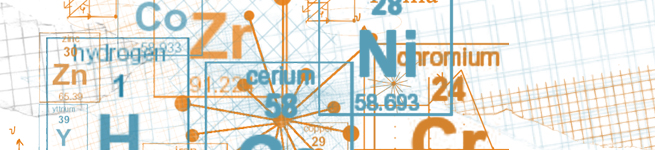
SYLOC-DEXA
System level optimization and control tools for diesel exhaust aftertreatment
Title of Programme
|
THE FIFTH FRAMEWORK PROGRAMME
COMPETITIVE AND SUSTAINABLE GROWTH (GROWTH)
PROGRAMME
|
Financing Code for Project
|
GRD1-1999-10588 |
Project start year - end year | 2000 - 2003 |
Financing organisation |
EUROPEAN COMMISSION
Research and Technological Development
(R & D Project)
|
Coordinator | |
Other partners |
Aerosol and Particle Technology Laboratory (APTL)
Politecnico di Torino (POLITO)
Zeuna-Staerker GmbH. & Co. KG
Johnoson Matthey plc (JM)
Clausthaler Umwelttechnik Institut GmbH (CUTEC)
Christian Doppler Laboratory for Applied Computational Thermofluiddynamics (CDL-ACT)
|
Budget / APTL Budget | 2,684,922 € / 289,946 € |
Scientific Manager / Project researcher | |
Project website | http://cordis.europa.eu/ |
Summary |
Background & policy context
The Diesel engine is the most efficient power plant among all known types of internal combustion engines. Passenger cars, heavy trucks, urban buses and industrial equipment are powered by Diesel engines all over the world. The Diesel engine is a major candidate to be the power plant of the future. However, there is a barrier to a wide-spread diffusion of Diesel engines: the contemporary reduction of NOx and particulate emissions up to the level required by the next stages of European legislation Euro 4 and beyond. Diesel particulates and nitrogen oxides, the two most troublesome components of Diesel exhaust emissions, have a dramatic, damaging impact on the environment and health.
In order to achieve proposed emission levels, considerable progress concerning the control of the combustion process using “second generation” common rail systems, characterised by higher fuel injection pressures and better electronic control of the injection process, has been made. Nevertheless, for vehicle classes of inertia test weight higher than 1.600 kg at present future emission levels can only be met by parallel application of catalysts and Diesel particulate filter systems.
Considerable attention therefore is currently directed towards improving the performance of these components. However, engine development work so far has proven that it is not possible to optimise the behaviour of the individual components of a Diesel engine exhaust system in isolation: the optimisation comes out from a fruitful interaction of individual elements of the exhaust system and the engine. The identification of successful combinations by building and testing entire aftertreatment systems or vehicles requires even more effort and money. Therefore it was the prime objective of the SYLOC-DEXA project to develop an alternative for the layout of optimal Diesel engine exhaust systems to meet future emission standards.
Objectives
The prime objective of the SYLOC-DEXA project to develop an alternative for the layout of optimal Diesel engine exhaust systems to meet future emission standards. T his alternative was seen to be the development of predictive computer models for the optimisation of complete Diesel engine exhaust systems and to use these models in such a way that various design options can be assessed rapidly to determine the most suitable design for a particular engine-prototype or vehicle.
In particular the project objectives have been:
Methodology
In the first half of the project, research work focused on laboratory experiments and steady-state engine tests for creating measurement data as input to the simulation software. The consortium partners have investigated practically all kinds of commercial particulate filter types and conversion systems. Filter sub-models, which account for pressure drop, filter regeneration characteristics and thermal behaviour, have been created and the models to represent the complete exhaust gas aftertreatment system have been developed. A database containing information on filter materials has been established and this was continuously updated/extended during the run-time of the project.
Research activities in the second half of the project concentrated on transient engine testing and model validation. In particular the layout of the exhaust system for a Demonstrator (Alfa Romeo 156 1.9 JTD ) was performed using the SYLOC-DEXA software toolkit to demonstrate its potential concerning filter loading and regeneration simulations. Additionally design variants of a virtual demonstrator have been assessed to show the wide range of applicability of the SYLOC-DEXA modules.
Furthermore two versions of the simulator toolkit have been created and made available to the project partners. The finally released software version V2.0 contains an efficient and user-friendly Graphical User Interface – GUI and sub-models to deal with all aspects of Diesel engine exhaust system design including oxidation catalysts and filter loading and regeneration modules.
Close co-operation between the consortium partners and intensive (and open) data exchange between the development engineers ensured a short reaction time with respect to the integration of new features in the modelling work, such as for example a reaction mechanism for the continuous soot regeneration provided by NO2.
|